Gyver Industries, Inc. (Gyver) would like to introduce ourselves in the area of treatment of oil and gas field produced industrial wastewater. During 2013 and 2014, Gyver was the principal engineering and design company as well as providing continuous construction oversight during the construction, installation, startup, and commissioning of a treatment facility constructed in Westwater, Utah, known as Harley Dome Production Water Recycling Facility (Harley Dome). Gyver developed the chemical pretreatment processes and recipes used on the wastewaters.
The Harley Dome facility was designed to receive trucked oil field produced wastewater from a large portion of western Colorado and eastern Utah. These trucked wastewaters came from many sources including: gas field wastewater; oil field wastewater; contained precipitation events; spent fracking solutions; wastewaters straight from the well head, from containment tanks, or ponds; and any other solution allowed to be treated under the Exemption of Oil and Gas Exploration and Production Wastes from Federal Hazardous Waste Regulations as published by the United States Environmental Protection Agency (EPA).
The system specified for the Harley Dome facility was to treat the received wastewaters to a quality that would allow a majority of the wastewaters to be surface discharged; meeting stream standard quality or better. The treated water was being reviewed for ownership and the owner/operator of the Harley Dome facility was investigating markets in which to sell this treated water. The treatment system was able to meet the National Pollutant Discharge Elimination System (NPDES) permit issued by the State of Utah and surface discharge was being conducted.
Contaminates within the wastewaters included; rocks, sand, gravel, sticks, miscellaneous debris, free oil, emulsified oil, volatile organic compounds (VOCs), various dissolved heavy metals, soaps, well treatment chemicals, ammonia, sulfides, chlorides, bacteria, etc.
The facility had previously installed two permitted injection wells. These injection wells were used for the disposal of received produced wastewater as well as the disposal of concentrated brine and wastewaters produced during the treatment process that could not be recycled. These injection wells were also used to dispose of wastewaters received by the facility that could not be treated due to their extremely high salts content and in some cases excessive soap residue from wells using soap sticks to dewater the production wells.
The facility was required to operate in all weather conditions; rain, sun, snow, wind, etc. and experienced temperatures extremes that ranged from minus 20° F to greater than 100° F. Ultra violet light and freeze protection were major concerns for exposed tanks and piping.
Utilities at the facility were limited to a; 200 Amp 220 VAC single phase electrical supply. The closest three phase electrical supply was more than five miles away and would have taken 2 to 5 years to get permitted with an estimated cost to install to the facility of five million dollars.
There was no potable water in the form of well or tap water available nor was there a natural gas supply available.
Due to power supply constraints at the site, electrical power for the operation of the treatment equipment was provided by diesel powered generators located at the facility. The electrical power from the generators is supplied through distribution panels that would allow the generators to be manually cycled between a smaller unit and a larger unit depending on power demands during operations.
Gyver assisted with the various environmental permitting requirements and inspections during construction to allow the facility to start operations while still under construction. The owner/operator eventually hired their own environmental compliance officer to manage these tasks.
During the design and construction phases of the facility, Gyver specified specific equipment to be used in the various required treatment processes to include; holding tanks, air stripping equipment, walnut shell filtration equipment, microfiltration equipment, transfer equipment, chemical supply and dosing equipment, granular activated carbon equipment, sludge management equipment, and reverse osmosis equipment.
Gyver designed the programmable logic control (PLC) system which was managed through a human machine interface (HMI) and built the control panels within Gyver’s shop. During the commissioning of the walnut shell filter (WSF), incorrect information from the manufacturer and their supplying different control parts resulted in the WSF control system being shorted out electrically. Gyver was able to design and program the controls for the WSF into our control system resulting in direct data feeds to our main control system.
During construction the owner bought a used gun barrel system that was added to the design to improve oil separation on the front end of the facility. Gyver was able to include this equipment in the design between the offloading stations and the main wastewater holding tanks.
By designing a bypass of the original wastewater holding tank, it was able to be designated as a receiving tank for untreatable wastewater that could be disposed by injection only.
Complex Stationary Oil Field Produced Wastewater Pretreatment System.
This system included the following processes: grit separation, oil separation, air stripping, down flow filtration through a walnut shell filter, chemical conversion, chemical precipitation of heavy metals, high shear mixing, solids separation, ceramic microfiltration, carbon absorption, sludge dewatering with a filter press, reverse osmosis, clean in place operations, permitted surface discharge including monitoring, coarse filtration by bag filter, and wastewater injection to a disposal well.
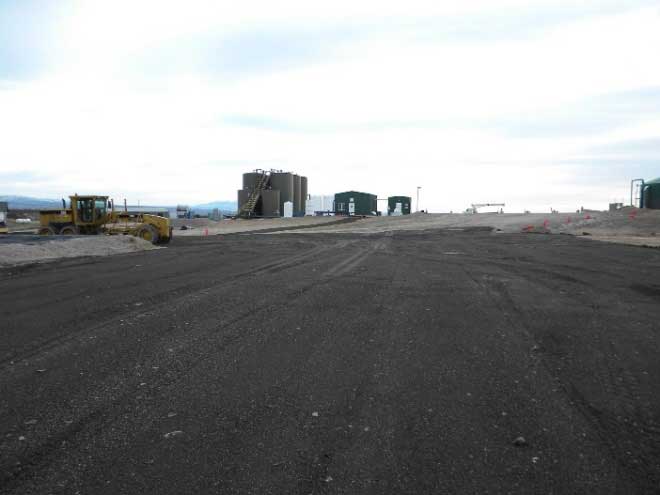
Produced Water Treatment Facility Offloading & Gun Barrel System
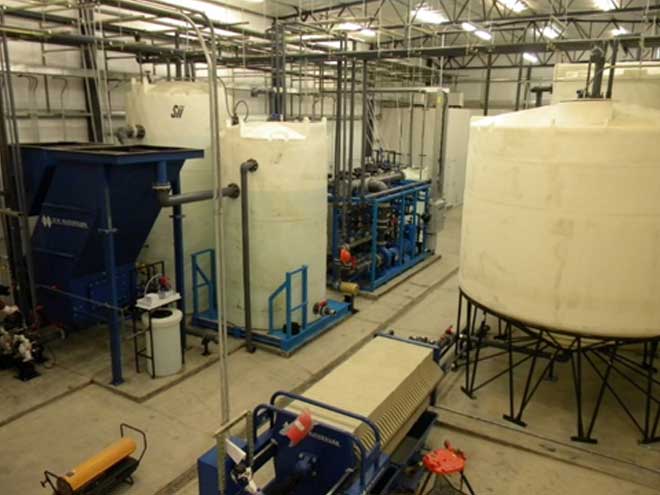
Produced Water Treatment Train, Side 1
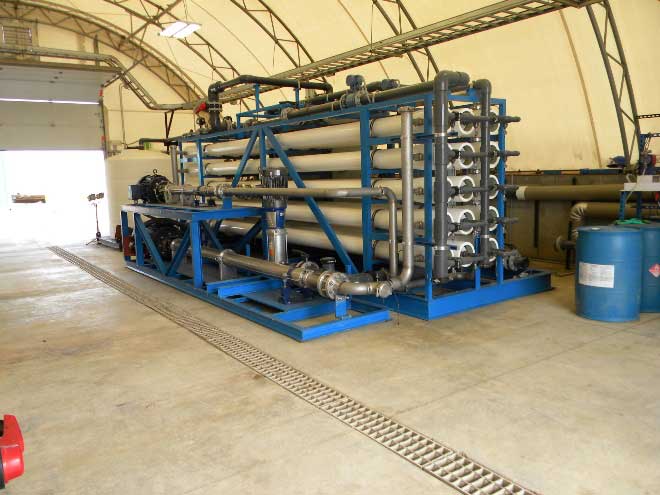
Produced Water Treatment RO System
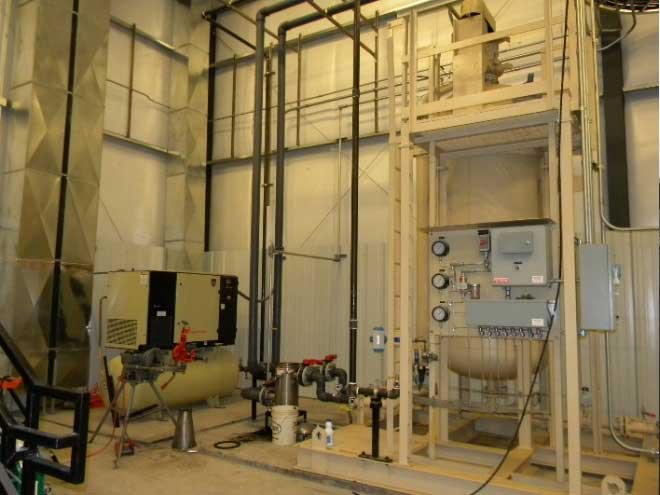
Walnut Shell Filtration System
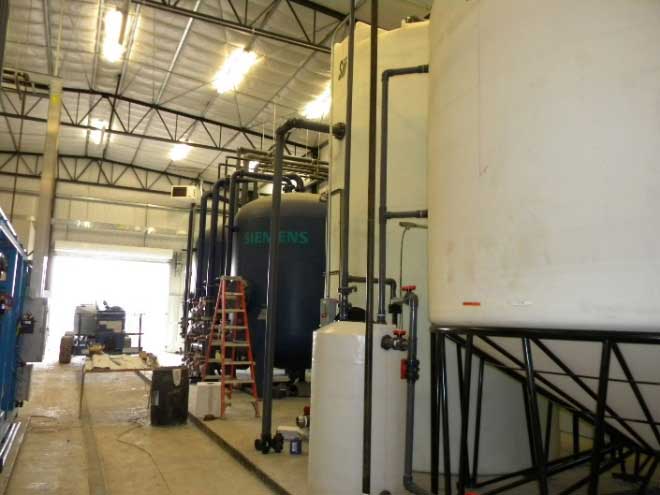
Produced Water Treatment Train, Side 2

Injection System Particulate Filtration
This facility was operational for approximately 16 months before being shut down for lack of supplied wastewater due to the turn down of the oilfields in that area.
Since working on the Harley Dome facility Gyver is in the developmental stage of a field pilot unit (pictured below) that will allow pilot testing at 15 to 30 gallons per minute of industrial wastewater with various pretreatment chemistries, and separation or filtration methods up to reverse osmosis. The unit is being built based on knowledge and experience acquired in treating wastewater from: plating shops, circuit board manufacturing, powder coating shops, specialty fastener manufacturing, acid mine drainage, wire manufacturing, food preparation equipment manufacturing, brewery wastewaters, petroleum produced wastewaters for surface discharge, and biological laboratory wastewater. Gyver is able to perform bench and pilot testing to determine the best and most economical treatment method for each individual wastewater stream. Gyver would like to offer a tour of this equipment if you are interested.
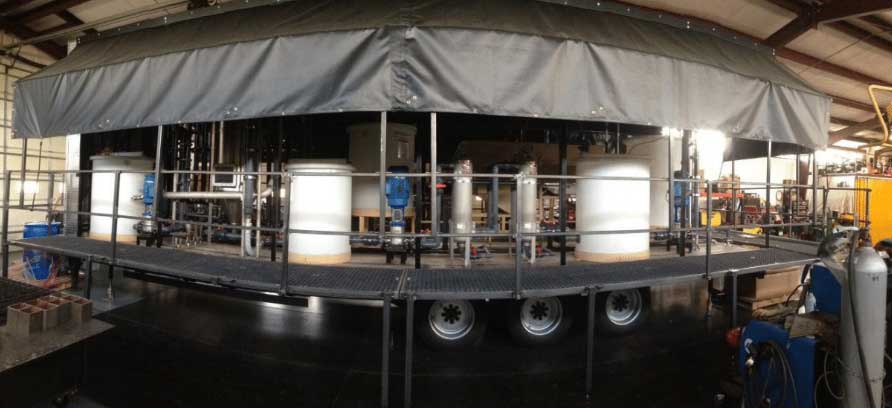
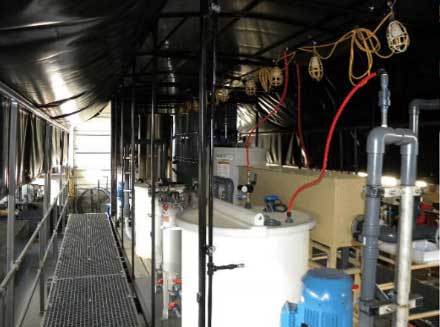
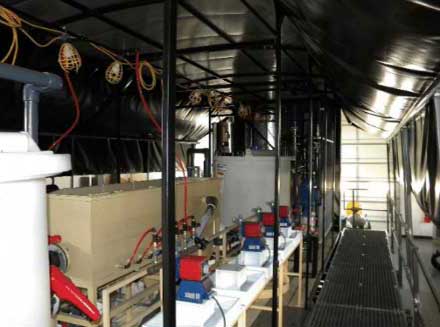
If your facility or project requires an industrial wastewater pretreatment system for any industrial wastewater stream to include oil or gas field produced wastewater, Gyver would welcome the opportunity to discuss your needs with you. If you have any questions or would like additional information please contact Gyver Industries at (970) 568-4220.
If your facility or project requires an industrial wastewater pretreatment system for any industrial wastewater stream to include oil or gas field produced wastewater, Gyver would welcome the opportunity to discuss your needs with you. If you have any questions or would like additional information please contact Gyver Industries at (970) 568-4220.
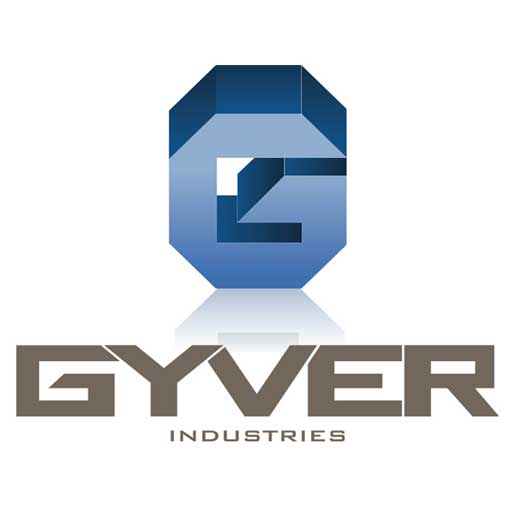